原创:广东特种设备安全Original Guangdong Special Equipment Safety Guangdong Special Equipment Safety 2020-12-31 17:50 Published in Guangdong
2020年7月12日8时55分左右,某金属材料有限公司员工叶某在操作一台电动葫芦桥式起重机吊运不锈钢钢卷的过程中,因误按起重机遥控装置按钮,导致其身体被挤压于两不锈钢钢卷之间,造成腹部受伤,经120医护人员现场抢救无效后死亡。该起事故造成1人死亡,直接经济损失约110万元。
At about 8:55 on July 12, 2020, Ye, an employee of a metal materials Co., Ltd., was operating an electric hoist overhead crane to lift stainless steel coils, and his body was squeezed between two stainless steel coils by mistake, causing his body to be squeezed between two stainless steel coils, resulting in abdominal injuries and death after 120 medical personnel failed to rescue him on the spot. The accident caused one death and a direct economic loss of about 1.1 million yuan.
根据《中华人民共和国特种设备安全法》等相关法律法规规定,经事故调查组调查分析认定,该起事故属于特种设备一般事故。
According to the “Special Equipment Safety Law of the People’s Republic of China” and other relevant laws and regulations, the accident investigation team investigated and analyzed that the accident was a general accident of special equipment.
(一)涉事起重机情况 (1) The situation of the crane involved
经现场勘验,涉事起重机为一台电动葫芦桥式起重机,型号规格:LHTG20-18.47-A3,额定起重量:20t,跨度:18.47m,起升高度:8.2m,工作级别:A3,大车运行速度:25m/min,小车运行速度:20m/min,出厂编号:201430199,出厂日期:2014年12月24日,注册代码:41904419002015040004,控制方式:遥控装置;涉事起重机在检验有效期内,有定期维护保养;现场试验其遥控装置控制功能,标识与起重机动作方向一致,急停开关有效,起吊与涉事不锈钢钢卷同规格同重量钢卷,起重机起升、下降、大车运行机构和小车运行机构制停动作正确,制动装置工作有效。
After on-site investigation, the crane involved is an electric hoist overhead crane, model specifications: LHTG20-18.47-A3, rated lifting capacity: 20t, span: 18.47m, lifting height: 8.2m, working level: A3, trolley running speed: 25m/min, trolley running speed: 20m/min, factory number: 201430199, factory date: December 24, 2014, Registration code: 41904419002015040004, control mode: remote control device; The crane involved had regular maintenance during the validity period of the inspection; The field test of the remote control device control function, the identification is consistent with the direction of the crane’s action, the emergency stop switch is effective, the lifting and the stainless steel coil involved in the same specification and weight of the steel coil, the crane lifting, descending, the trolley running mechanism and the trolley running mechanism make the stop action correct, and the braking device works effectively.
(二)现场视频监控情况 (2) On-site video surveillance
1.8时53分09秒,叶某在车间通过起重机遥控装置操作涉事起重机将不锈钢钢卷从电动抬车吊运至该车间重卷存放区;
At 1.8:53:09, Ye operated the crane involved in the workshop through the crane remote control device to lift the stainless steel coil from the electric lift truck to the recoiling storage area of the workshop;
2.8时55分29秒,叶某操作涉事起重机遥控装置将不锈钢钢卷运至重卷存放区并在钢卷下方铺设防滑布;
2. At 8:55:29, Ye operated the remote control device of the crane involved to transport the stainless steel coil to the recoil storage area and lay an anti-slip cloth under the coil;
3.8时55分43秒,在铺设好防滑布之后,叶某进入吊运钢卷与A钢卷之间。此时,叶某左手扶吊运钢卷,右手持遥控装置。根据事发后现场测量推算,此时两钢卷间距为0.54m;
3.8:55:43, after laying the non-slip cloth, Ye entered between the hoisting steel coil and the A steel coil. At this time, Ye lifted the steel coil with his left hand and held the remote control device with his right hand. According to the on-site measurement after the incident, the distance between the two steel coils was 0.54m;
4.8时55分44秒,叶某通过涉事起重机遥控装置将起重机重新启动,向北侧运行,此时叶某被吊运钢卷碰撞并推向A钢卷,由于A钢卷已固定放置在地面托架上,因此A钢卷无法移动。8时55分45秒起重机继续向北侧移动,并将叶某挤压在吊运钢卷与A钢卷之间;
At 4.8:55:44, Ye restarted the crane through the remote control device of the crane involved and ran to the north side, at this time Ye was hit by the lifting steel coil and pushed to the A steel coil, because the A steel coil has been fixed on the ground bracket, so the A steel coil cannot be moved. At 8:55:45, the crane continued to move to the north side, and squeezed Ye between the hoisting steel coil and the A steel coil;
5.8时55分46秒,挤压过程结束,叶某倒地。 At 5.8:55:46, the squeezing process ended, and Ye fell to the ground.
(三)调查询问情况 (3) Investigation and inquiry
1.叶某是涉事公司压延机辅助工,负责重卷钢带生产,因工作需要需操作起重机吊运钢卷,未持特种设备作业人员证和安全管理人员证;
1. Ye is an auxiliary worker of the calender of the company involved, responsible for the production of recoiled steel strips, and needs to operate a crane to lift steel coils due to work needs, and does not hold a special equipment operator certificate and a safety management personnel certificate;
2.涉事公司未对叶某进行系统全面的起重机械安全警示教育和技能培训,事发时,涉事公司未对叶某起重机操作行为进行有效监督;
2. The company involved did not carry out systematic and comprehensive safety warning education and skills training for Ye’s lifting machinery, and at the time of the incident, the company involved did not effectively supervise Ye’s crane operation;
3.涉事公司编制了起重机械安全管理制度,但该制度无编制、审核、批准人员签名和发布日期;
3. The company involved has prepared a safety management system for lifting machinery, but the system does not have the signature and release date of the personnel who prepare, review and approve it;
4.涉事公司分管安全生产的主要负责人为该公司副总经理,为公司特种设备安全主要负责人。
4. The main person in charge of safety production of the company involved is the deputy general manager of the company and the main person in charge of the safety of the company’s special equipment.
(一)事故原因分析 (1) Analysis of the cause of the accident
1.叶某违规操作:叶某在吊运钢卷过程中未能有效识别危险源及危险距离,其在操作涉事起重机的过程中左手手扶吊运钢卷,右手手持遥控装置,进入了吊运钢卷与旁边另一静止放置的钢卷之间的狭小区域,未保持足够的安全距离,造成对起重机械的误动作,其操作行为不符合《起重机械安全规程》(GB/T6067.1-2010)第17.1a):“司机操作起重机时,不允许从事分散注意力的其他操作”、17.2.5g):“起重机械进行回转、变幅和运行时,要避免突然的启动和停止”和17.2.5a):“载荷在运行轨迹上应与障碍物保持一定的间距”等相关规定要求,其操作行为属于违规操作。
1. Ye’s illegal operation: Ye failed to effectively identify the source of danger and the dangerous distance in the process of lifting the steel coil, and in the process of operating the crane involved, he held the steel coil with his left hand, and held the remote control device with his right hand, and entered the narrow area between the lifting steel coil and another statically placed steel coil next to it, and did not maintain a sufficient safety distance, resulting in a misoperation of the lifting machinery, and his operation behavior did not comply with Article 17.1a of the “Safety Regulations for Lifting Machinery” (GB/T6067.1-2010): ” When the driver operates the crane, it is not allowed to engage in other distracting operations”, 17.2.5g): “When the lifting machinery is rotating, luffing and running, it is necessary to avoid sudden start and stop” and 17.2.5a): “The load should be kept at a certain distance from the obstacle on the running trajectory” and other relevant regulations, and its operation behavior is an illegal operation.
2.涉事公司起重机械安全管理不到位:根据《中华人民共和国特种设备安全法》第十三条规定:“特种设备使用单位应当按照国家有关规定配备特种设备作业人员,并对其进行必要的安全教育和技能培训”,涉事公司未对叶某进行全面系统的起重机械安全警示教育和技能培训;起重机械安全管理制度无相关编制、审核、批准人员的签名及相关编制发布日期;车间内无张贴起重机械作业的相关操作规程;叶某在违规操作涉事起重机械时,公司未能及时发现并对其违规行为进行制止。
2. The safety management of lifting machinery of the company involved is not in place: according to Article 13 of the Special Equipment Safety Law of the People’s Republic of China, “the special equipment user shall be equipped with special equipment operators in accordance with relevant national regulations, and carry out necessary safety education and skill training”, the company involved did not carry out comprehensive and systematic safety warning education and skill training for Ye; The hoisting machinery safety management system does not have the signatures of the relevant preparation, review and approval personnel and the relevant preparation and release date; There are no relevant operating procedures for hoisting machinery operations posted in the workshop; When Ye operated the lifting machinery involved in violation of regulations, the company failed to discover and stop his violations in time.
(二)事故直接原因 (2) The direct cause of the accident
叶某在操作涉事起重机吊运钢卷的过程中,采用了单手操作的方式,因操作失误,其身体被挤压于被吊运钢卷与另一静止放置在地面的钢卷之间,导致事故发生。
In the process of operating the crane involved in the lifting of the steel coil, Ye adopted a one-handed operation method, and due to the operation error, his body was squeezed between the lifted steel coil and another steel coil placed on the ground, resulting in the accident.
(三)事故间接原因 (3) Indirect causes of the accident
1.涉事公司起重机械安全管理不到位,未对叶某进行系统全面的起重机械安全警示教育及技能培训,未对叶某违规操作行为进行有效监督并及时制止;
1. The safety management of lifting machinery of the company involved was not in place, and Ye was not systematically and comprehensively trained in safety warning education and skills for lifting machinery, and Ye’s illegal operation was not effectively supervised and stopped in a timely manner;
2.叶某安全意识淡薄,其在操作起重机械的过程中,进入了被吊运钢卷与旁边另一静止放置在地面的钢卷之间的狭小区域,未保持足够的安全距离。
2. Ye had a weak sense of safety, and in the process of operating the lifting machinery, he entered a narrow area between the steel coil being lifted and another steel coil placed on the ground next to him, and did not maintain a sufficient safety distance.
(四)事故主要原因 (4) The main cause of the accident
1.作业人员违规操作; 1. Illegal operation of operators;
2.起重机械使用单位安全管理不到位。 2. The safety management of the lifting machinery user unit is not in place.
(五)事故次要原因 (5) Secondary causes of the accident
1.该公司相关管理人员安全管理不到位。 1. The safety management of the company’s relevant management personnel is not in place.
2.作业人员违规操作,安全意识淡薄。 2. Operators operate in violation of regulations and have weak safety awareness.
根据《中华人民共和国特种设备安全法》相关规定,由特种设备安全监察部门和有关部门对造成本次事故发生负有责任的单位和个人依法进行处理。责令涉事单位遵照有关法律法规、安全技术规范的要求按“四不放过”原则提交整改报告。
According to the relevant provisions of the Special Equipment Safety Law of the People’s Republic of China, the special equipment safety supervision department and relevant departments shall deal with the units and individuals responsible for the occurrence of this accident in accordance with the law. Order the units involved to submit rectification reports in accordance with the requirements of relevant laws, regulations, and safety technical specifications in accordance with the principle of “four don’t let go”.
针对此次事故教训,建议涉事公司要认真吸取事故教训,必须高度重视起重机械等特种设备安全管理工作。
In view of the lessons of this accident, it is suggested that the companies involved should seriously learn the lessons of the accident and must attach great importance to the safety management of special equipment such as lifting machinery.
(一)严格落实企业安全主体责任。做好事故相关责任人员的处理,并及时将责任人员处理结果和整改情况书面报告事故调查组。
(1) Strictly implement the main responsibility for enterprise security. Do a good job in handling the relevant responsible personnel of the accident, and promptly report the results of the handling and rectification of the responsible personnel to the accident investigation team in writing.
(二)完善安全管理制度和安全操作规程。依法履行特种设备安全主体责任,加强对起重机械作业人员的安全警示教育和技能培训,建立健全起重机械安全管理制度,明确岗位职责,制定科学合理的安全操作规程,督促监督作业人员按章操作,确保起重机械使用安全。
(2) Improve the safety management system and safety operation procedures. Fulfill the main responsibility for the safety of special equipment in accordance with the law, strengthen the safety warning education and skill training of lifting machinery operators, establish and improve the safety management system of lifting machinery, clarify job responsibilities, formulate scientific and reasonable safety operation procedures, and supervise and supervise operators to operate according to regulations to ensure the safety of lifting machinery.
(三)加大起重机械安全宣传力度。提高起重机械使用单位的安全意识和管理水平,推动企业落实安全主体责任,提高起重机械从业人员技能水平和安全防范意识。
(3) Increase the safety publicity of lifting machinery. Improve the safety awareness and management level of lifting machinery users, promote enterprises to implement the main responsibility of safety, and improve the skill level and safety awareness of lifting machinery practitioners.
(四)立即组织开展特种设备安全隐患自查自纠。全面排查特种设备安全方面存在的问题,及时消除特种设备安全隐患;加强特种设备日常维护和定期检查,确保特种设备安全可靠;加强对特种设备作业人员进行安全警示教育和技能培训,保证特种设备的作业人员具备必要的安全知识;公司负责人和管理人员要切实提高安全管理水平,加强安全风险防控意识;严格落实安全管理制度和岗位责任制;全公司通报事故相关责任人员处理结果,全员开展事故警示教育。
(4) Immediately organize and carry out self-inspection and self-correction of potential safety hazards of special equipment. Comprehensively investigate the problems existing in the safety of special equipment, and eliminate the potential safety hazards of special equipment in a timely manner; Strengthen the daily maintenance and regular inspection of special equipment to ensure the safety and reliability of special equipment; Strengthen safety warning education and skills training for special equipment operators to ensure that special equipment operators have the necessary safety knowledge; The person in charge and management personnel of the company should effectively improve the level of safety management and strengthen the awareness of safety risk prevention and control; Strictly implement the safety management system and post responsibility system; The whole company reports the results of the handling of the relevant personnel responsible for the accident, and all employees carry out accident warning education.
同时,各地特种设备安全监督管理部门应加强对特种设备使用单位的安全警示教育,宣讲相关法律法规,通报事故情况,引以为戒,吸取事故教训,提高企业安全主体责任认识。
At the same time, the special equipment safety supervision and management departments should strengthen the safety warning education of special equipment users, preach relevant laws and regulations, report the accident, take it as a warning, learn lessons from the accident, and improve the awareness of the main responsibility of enterprise safety.
图1 涉事起重机 Figure 1 The crane involved
图2 事发时吊运的钢卷 Fig.2 Steel coils lifted at the time of the incident
图3事故现场 Figure 3: The scene of the accident
图4 初始起吊位置 Fig.4. Initial lifting position
图5 进入重卷存放区 Figure 5 Entering the reroll storage area
图6 进入起吊钢卷与固定钢卷之间 Fig.6 Between the hoisting coil and the fixed coil
图7 当事人被挤压 Figure 7 The parties were squeezed
图8 当事人被挤压后倒地 Fig.8 The person fell to the ground after being squeezed
文章来源:广东特种设备安全 Article source: Guangdong Special Equipment Safety
文章来源:广东特种设备安全”
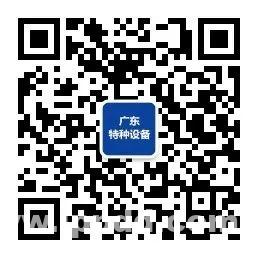